行业应用实例-含能材料
炸药,火箭、导弹、弹药和烟火装置等这些材料是许多不同化学物质的复杂混合物,形成的产品包括粉末、粘性糊状物、高粘性糊状物和液体,每一种都必须按照严格的标准制造。在含能材料的性能和致命性方面建立可量化的增益,以及改进制造方法,提高制造安全性,降低成本,并减轻高能材料制造对环境的影响等这些研究发展下所追逐的问题点也是蜂鸟声共振(HAM)技术所与之适配的。
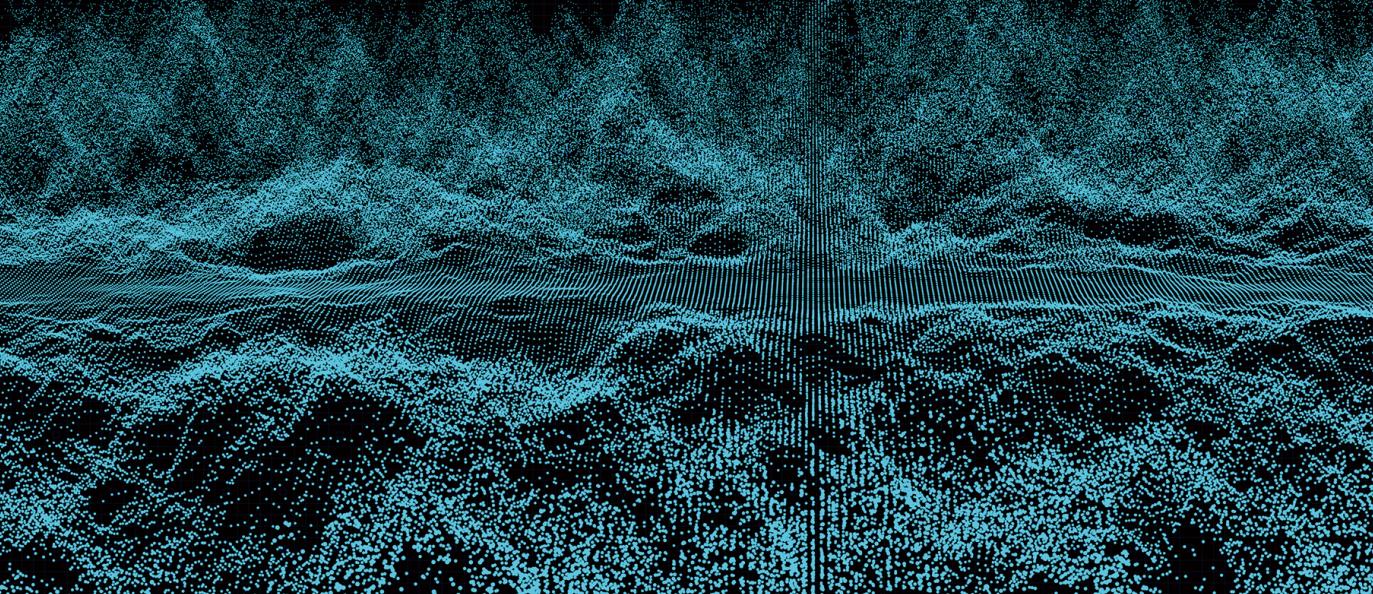
行业应用实例-含能材料
炸药,火箭、导弹、弹药和烟火装置等这些材料是许多不同化学物质的复杂混合物,形成的产品包括粉末、粘性糊状物、高粘性糊状物和液体,每一种都必须按照严格的标准制造。在含能材料的性能和致命性方面建立可量化的增益,以及改进制造方法,提高制造安全性,降低成本,并减轻高能材料制造对环境的影响等这些研究发展下所追逐的问题点也是蜂鸟声共振(HAM)技术所与之适配的。
共振声混合器中的初级爆炸过程
用于大批量生产烟火的更安全的声共振混合方法
浇铸固化和声共振混合推进剂工艺的比较
用声共振混合技术处理含能材料的研究
高负荷凝胶推进剂的合成